以代工為主的電子產品制造服務(EMS)環節的利潤率越來越低,PCBA代工的質量保證要求卻越來越高,根據SPC統計故障概率譜來設計工藝測試的工序點,借助一定的組裝檢測儀器設備來監控制程合適,是保證PCBA加工質量檢測和改進提升的重要環節。對于許多中小型電子制造代工廠已無力投資增添高額成本的組裝檢測儀器設備,采用功能測試設計(Functional Tester Design)來保證PCBA加工品質,是一種性價比較高的措施手段,廣泛應用于小批量多品種外協加工生產測試過程中。
1 引言
電子制造代工作為比較成熟的加工制造方式正在進入微利時代, PCBA代工的利潤率是越來越低,PCBA代工的質量保證要求卻越來越高。
在PCBA加工中的一個基本要求是一致性、正確性,對于差異要控制,變異不允許。在組裝制造過程中的品質不良有設計問題、材料問題、組裝問題三個方面,前兩項需預先采取措施防止其發生,組裝過程中的問題象缺件、損件、錯件、偏移等大部分是可以目視檢查的,但是焊接質量很難用目視的方法來完全判定,而且有時會出現PCBA交付在顧客處的炸機、爆板、功能不良等故障。
根據中國賽寶實驗室可靠性研究分析中心提供的PCBA電裝品質問題分析統計,主要的組裝失效模式為焊接不良,占所有組裝不良問題的57%,如圖1所示??梢娊^大多數產品品質問題是由組裝焊接過程焊點故障引起的。
電裝不良統計圖
隨著PCBA的設計趨于小型化,更小的器件,更小的間距,電子組裝件的微型化(高密集度)越來越多,引起PCBA的焊點缺陷、檢測定位困難、可視性及可維修性差,甚至不可修復潛在失效風險也隨之增加。
僅從組裝過程的傳統目視檢查控制不能完全剔除焊接不良,還需要進行自動X射線無損檢測,在長三角、珠三角、還有軍工生產中已經推廣應用,效果十分好。但是增添設備的投資較大,本來勞動力成本連年遞增已經讓許多中小型電子制造代工廠叫苦不迭,再加上顧客對加工品質的不斷要求,實力不強的代工廠已無力增添高額成本檢測手段。
2 生產測試技術
目前在電子組裝測試領域中使用的測試技術種類繁多,常用的有人工目視檢查(Manual Visual Inspection,簡稱MVI)、在線測試(In-CircuitTester,簡稱 ICT)、自動光學測試(AutomaticOptical Inspection,簡稱 AOI)、自動 X 射線測試(AutomaticX-ray Inspection,簡稱AXI)、功能測試(Functional Tester,簡稱 FCT)等。
它們可以根據PCBA是否通過加電歸為兩大類:一種是電氣測試技術,一種是非電氣測試技術;也可以根據PCBA是否和測試設備接觸分為兩大類:一種是接觸式測試技術,一種是非接觸式測試技術。見表1,供參考。
2.1 人工目視MVI
人工目視測試是通過人的視覺比較來確認PCBA上的元器件貼裝、插裝、焊接質量。靠操作者的眼睛看或輔以放大鏡、顯微鏡目視。這種技術是使用最久遠和最廣泛的在線測試方法之一,圖1所示。
人工目視檢查
但是隨著微電子表面組裝技術(SMT)的應用發展,電子產品朝輕薄小型化方向發展,印制板組件(PCBA)的密度隨著元器件的不斷微型化變得越來越高。密集插裝元器件的相互阻擋視線,還有近幾年廣泛出現的微封裝(0201) 、“不可見”焊點( 如BGA、 CSP 和倒裝晶片組件FCA),人工目視“查顏觀色”的方法肉眼已無能為力,已經無法保證PCBA加工的品質。
曾經有人進行過這樣的試驗,讓四位經驗豐富的檢驗員對同一塊板子(中等復雜程度的線路板,如300個元件、3500個節點的單面板)的焊點質量分別作四次檢驗。結果是,第一位檢驗員查出了其中百分之四十四的缺陷,第二位檢驗員和第一位的結果有百分之二十八的一致性,第三位檢驗員和前二位有百分之十二的一致性,而第四位檢驗員和前三位只有百分之六的一致性。
這一試驗暴露了人工目檢的主觀性,目檢既不可靠也不經濟。
目前在代工制造中,人工目視測試方法僅作為補充的輔助方法來使用。
2.2 在線測試ICT
在線測試儀(ICT),也稱飛針(探針、針床)測試儀,圖2所示。它的原理是通過對組裝完成的PCBA在板元器件的電性能及電氣連接進行測試來檢查生產制造缺陷及元器件不良的一種測試技術手段。
一種ICT測試儀
在線測試儀測量時使用專門的飛針(探針、針床)與已焊接好的線路板上的元器件接觸,并用數百毫伏電壓和10毫安以內電流進行分立隔離測試,從而精確地測出所裝電阻、電感、電容、二極管、三極管、可控硅、場效應管、集成塊等通用和特殊元器件的漏裝、錯裝、參數值偏差、焊點連焊、線路板開短路等故障,并將故障是哪個元件或開短路位于哪個點準確定位。
飛針測試最大的優點是市場反應速度快,但檢測速度慢,適合測試樣板和小批量訂單。若是顧客要求打樣品,可選擇飛針測試,直到顧客做大批量訂單時再改做針床測試,這樣免去了顧客更改過程或撤銷訂單的針床制作成本投入。
ICT 的長處是電氣缺陷測試,如器件的功能不正?;蝈e值。在線測試能夠有效地查找組裝過程中發生的各種缺陷和故障,但它不能完整評估PCBA的電氣性能。
ICT需要顧客的PCB設計符合ICT可測試性設計要求,對于代工顧客的的多樣化層次實施起來較為麻煩。另外,PCBA測試的節點數越多,成本將急劇增長,主要是消耗在針床或飛針設計制造上,而且會存在下針測試困難的挑戰。當節點數超過ICT的要求時,當PCBA的物理尺寸超過ICT要求時,問題將更難解決。
電子產品的小型化發展趨勢直接導致了PCBA的設計微型化(高密集度) 組裝,PCB設計對于ICT 測試節點僅留有很小的空間,甚至被取消,ICT測試的價值將隨之消失。這就意味著生產制造將面臨大量的潛在問題,PCBA加工完成直接進入終檢,不僅會導致合格率的下降、返修量與故障診斷費用的增加,而且會造成生產的延誤。
2.3 自動光學測試AOI
自動光學測試也稱為自動視覺測試,圖3所示。它的原理是機器通過攝像頭自動掃描PCBA,將PCBA上元器件及焊接特征(貼片元器件狀態、焊點形態及缺陷)捕捉成圖像,通過軟件處理,與數據庫中合格的參數進行綜合比較,判斷這一元器件及其狀態是否完好,然后得出檢測結果。
AOI可以檢查出PCBA上缺陷諸如錫膏印刷、元器件貼裝(元器件缺失、極性反轉)、回流焊接(橋接、或者焊點質量問題),并通過顯示器或自動標志把缺陷顯示/標示出來,供維修人員修理用。
AOI測試儀
這種測試技術是一種非電氣的、無夾具的測試技術,對短路識別較差,不能檢測電路錯誤,同時對不可見焊點的檢測也無能為力。通常AOI工藝設計的SMT產線工序點有三處,錫膏印刷之后、回流焊前、回流焊后,如圖4所示,可根據公司的具體需要選擇。AOI測試的檢測前置,起到的預防缺陷作用越明顯。從總的使用效果來講,AOI對SMT測試較好,對THT作用較差。
AOI技術的優勢是對元器件貼裝位置快速有效的測試。但是也有其不足和所面臨的挑戰:
(1)元器件的微型化
0402、0201甚至01005器件的逐步應用使焊點檢測變得越來越困難。因為焊盤外露長度A在不斷減小,甚至可能消失,這會造成器件定位不準及焊點不可檢。如圖4所示。
焊點不可檢
(2)PCB的微型化(高密集度)
由于PCB設計的高密集度導致出現高矮器件相鄰的陰影效應,小器件的一邊焊點由于太靠近高器件,高器件擋住入射光而使這些焊點比較暗,如圖5所示;二次反射光造成的偏色效應,小器件對稱排放的間距小到一定值后,入射的紅光(R)會使跟其對稱的焊盤中間的紅色偏多,如圖6所示。AOI在測試這些焊點時會產生很多誤報。
2.4 自動X射線測試AXI
X射線測試儀AXI如圖7所示,組裝好的PCBA沿導軌進入機器內部后,位于PCBA上方的X-Ray發射管發射X射線穿過線路板后被置于下方的探測器(一般為攝像機)接受,由于焊點中含有可以大量吸收X射線的錫鉛金屬元素,因此與穿過PCB玻璃纖維的X射線相比,照射在焊點上的X射線被大量吸收,而呈黑點產生良好圖像,使得對焊點的分析變得相當直觀,故簡單的圖像分析算法便可自動且可靠地檢驗焊點缺陷。X射線透視圖可以顯示焊點厚度,形狀及質量的密度分布。這些指針能充分反映出焊點的焊接質量,包括開路、短路、孔、洞、內部氣泡以及錫量不足,并能做到定量分析。
一種X射線測試儀AXI
X射線測試技術有兩種方式,一種是2D或透射X射線測試法,這與簡單的X射線胸透類似。對于單面PCBA焊點的測試,板上元器件的焊點可產生清晰的視像。另一種是斷層或3D X射線測試法,目前PCBA制造商正在使用的、可實現3D X射線檢驗的技術被稱作X射線斷層照像機。X射線斷層照像機之所以能夠測試雙面PCBA,因為它可以對兩側的焊點獨立成像。還可對那些不可見焊點如BGA(BallGridArry,焊球陳列)等進行多層圖像"切片"檢測,即對BGA焊接連接處的頂部、中部和底部進行徹底檢測。同進利用此方法還可測通孔(PTH)焊點,檢查通孔中焊料是否充實,從而極大地提高焊點連接質量,避免過早失效。
這種測試技術是一種非電氣的、無夾具的測試技術,一般設計工序放置點在焊接全部完成之后。AXI技術的優勢是對焊接性能進行綜合測試,避免焊點早期失效,提高品質可靠性,特別是對不可見焊點的檢測。但不能測試電路電氣性能方面的缺陷和故障,對于元器件的極性、方向測試能力不足,還面臨開焊測試不能檢出的挑戰。
盡管ICT 和FCT 能夠檢測出封裝器件引腳與焊盤間的電氣連接是否有效,但這些技術卻不能檢驗出品質低劣和/ 或可能產生過早失效的焊點。隨著ICT的消失,取而代之可用AXI,保持較高的組裝效率,并減少故障診斷與返修工作,使送到終檢的PCBA良率大大提高。當然,由于AXI的價格昂貴,對于那些無力購置檢測設備的廠家,可采用功能測試設計來彌補解決。
BGA焊點的3D X射線檢測能顯示出氣孔和不充實的焊點
2.5 功能測試FCT
功能測試的基本原理是將組裝完成的PCBA作為一個功能體,使其處于所構成的完整產品中,看其整機的所有功能和電氣性能是否滿足要求,藉此來評價PCBA的組裝品質。對其提供輸入信號,按照設計要求檢測輸出信號,包括電壓、電流、波形等。這種測試是為了確保PCBA能否按照設計要求正常工作。
這種技術方法簡單、投資可多可少,可以采用單片機控制設計成較為專業的自動功能測試儀,也可以自行設計成簡易手動控制的專用功能測試儀。功能測試的缺點是不具有自動診斷故障和故障準確定位,只能確定故障的大致范圍,維修還要靠技術分析和經驗進行。
2.6 幾種測試技術的比較
在電子組裝行業,電子元器件及電子組件的微型化開始普及,微型的BGA、POP、01005,這個變化對組裝工藝測試設計提出了挑戰,特別是工藝測試設備(AOI、AXI、ICT)在測試的諸多方面遇到了挑戰,如微型化(高密集度)PCBA給ICT夾具制造帶來較大沖擊,AOI設備的設計使其無法檢測到藏于組件下面的引腳或焊接狀況,BGA器件的引腳全部排放在器件底部,特別是對于帶金屬屏蔽的BGA,對于無引出線的多層電路板的BGA,使得ICT力所不能及等。此外,AOI、AXI這兩種設備的測試還受到來料變化、焊點形態變化等影響,最終都會影響其檢出率,不能很好地滿足要求。
所以很難界定哪些技術手段是組裝業所必須的,而哪些是不需要的,每種測試技術的應用領域和測試手段都不盡相同,都有其測試的側重點,主要是根據工廠實力和承受能力來實施。從近幾年的發展趨勢來看,測試技術方法選擇的主要依據應該著眼于PCBA組件和工藝的類型、故障概率譜和對產品可靠性的要求,使用兩種或以上測試技術手段并用、互為補充乃是最佳途徑。
各種組裝測試的效能統計比較數據如表1,充分說明了不能靠單一的測試技術手段。
深圳宏力捷推薦服務:PCB設計打樣 | PCB抄板打樣 | PCB打樣&批量生產 | PCBA代工代料
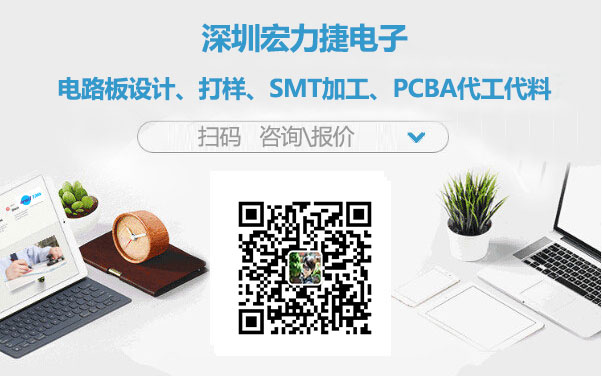