摘要:當前電子產品日新月異,要求電路板高密度組裝,安裝方式由表面安裝(SMT)取代通孔插裝(THT)已是歷史的必然,因此,印制板技術正向高密度、多層化方向飛速發展。而印制板的合理設計是SMT技術中的關鍵,也是SMT工藝質量的保證,并有助于提高生產效率。本文就表面安裝PCB設計時需考慮的一些制造工藝性問題進行了闡述,給
PCB設計人員提供一個參考。
1、前言
隨著通信﹑電子類產品的市場競爭不斷加劇,產品的生命周期在不斷縮短,企業原有產品的升級及新產品的投放速度對該企業的生存和發展起到越來越關鍵的作用。而在制造環節,如何在生產中用更少的導入時間獲得更高可制造性和制造質量的新產品越來越成為有識之士所追求的核心競爭力。
在電子產品的制造中,隨著產品的微型化﹑復雜化,電路板的組裝密度越來越高,相應產生并獲得廣泛使用的新一代SMT裝聯工藝,要求設計者在一開始,就必須考慮到可制造性。一旦在設計時考慮不周導致可制造性差,勢必要修改設計,必然會延長產品的導入時間和增加導入成本,即使對PCB布局進行微小的改動,重新制做印制板和SMT焊膏印刷網板的費用高達數千甚至上萬元以上,對模擬電路甚至要重新進行調試。而延誤了導入時間可能使企業在市場上錯失良機,在戰略上處于非常不利的位置。但如果不進行修改而勉強生產,必然使產品存在制造缺陷,或使制造成本猛增,所付出的代價將更大。所以,在企業進行新產品設計時,越早考慮設計的可制造性問題,越有利于新產品的有效導入。
2、PCB設計時考慮的內容
PCB設計的可制造性分為兩類,一是指生產印制電路板的加工工藝性;二是指電路及結構上的元器件和印制電路板的裝聯工藝性。對生產印制電路板的加工工藝性,一般的
PCB制作廠家,由于受其制造能力的影響,會非常詳細的給設計人員提供相關的要求,在實際中相對應用情況較好,而根據筆者的了解,真正在實際中沒有受到足夠重視的,是第二類,即面向PCBA裝聯的可制造性設計。本文的重點也在于描述在PCB設計的階段,設計者必需考慮的可制造性問題。
面向
PCBA裝聯的可制造性設計要求PCB設計者在設計PCB的初期就考慮以下內容:
2.1 恰當的選擇組裝方式及元件布局
組裝方式的選擇及元件布局是PCB可制造性一個非常重要的方面,對裝聯效率及成本﹑產品質量影響極大,而實際上筆者接觸過相當多的PCB,在一些很基本的原則方面考慮也尚有欠缺。
(1) 選擇合適的組裝方式
通常針對PCB不同的裝聯密度,推薦的組裝方式有以下幾種:
作為一名電路設計工程師,應該對所設計PCB的裝聯工序流程有一個正確的認識,這樣就可以避免犯一些原則性的錯誤。在選擇組裝方式時,除考慮PCB的組裝密度,布線的難易外,必須還要根據此組裝方式的典型工藝流程,考慮到企業本身的工藝設備水平。倘若本企業沒有較好的波峰焊接工藝,那么選擇上表中的第五種組裝方式可能會給自己帶來很大的麻煩。另外值得注意的一點是,若計劃對焊接面實施波峰焊接工藝,應避免焊接面上布置有少數幾個SMD而造成工藝復雜化。
(2) 元器件布局
PCB上元器件的布局對生產效率和成本有相當重要的影響,是衡量PCB設計的可裝聯性的重要指標。一般來講,元器件盡可能均勻地、有規則地、整齊排列,并按相同方向、極性分布排列。有規則的排列方便檢查,有利于提高貼片/插件速度,均勻分布利于散熱和焊接工藝的優化。另一方面,為簡化工藝流程,PCB設計者始終都要清楚,在PCB的任一面,只能采用回流焊接和波峰焊接中的一種群焊工藝。這點在組裝密度較大、PCB的焊接面必須分布較多貼片元器件時,尤其值得注意。設計者要考慮對焊接面上的貼裝元件使用何種群焊工藝,最為優選的是使用貼片固化后的波峰焊工藝,可以同時對元件面上的穿孔器件的引腳進行焊接;但波峰焊接貼片元件有相對嚴格的約束,只能焊接0603及以上尺寸的片式阻容﹑SOT﹑SOIC(引腳間距≥1mm且高度小于2.0mm)。分布在焊接面的元器件,引腳的方向宜垂直于波峰焊接時PCB的傳送方向,以保證元器件兩邊的焊端或引線同時被浸焊,相鄰元件間的排列次序和間距也應滿足波峰焊接的要求以避免“遮蔽效應”。當采用波峰焊接SOIC等多腳元件時,應于錫流方向最后兩個(每邊各1)焊腳處設置竊錫焊盤,防止連焊。
類型相似的元件應該以相同的方向排列在板上,使得元件的貼裝、檢查和焊接更容易。例如使所有徑向電容的負極朝向板件的右面,使所有雙列直插封裝(DIP)的缺口標記面向同一方向等等,這樣可以加快插裝的速度并更易于發現錯誤。如圖2所示,由于A板采用了這種方法,所以能很容易地找到反向電容器,而B板查找則需要用較多時間。實際上一個公司可以對其制造的所有線路板元件方向進行標準化處理,某些板子的布局可能不一定允許這樣做,但這應該是一個努力的方向。
還有,相似的元件類型應該盡可能接地在一起,所有元件的第一腳在同一個方向。
但筆者確實遇見過相當多的PCB,組裝密度過大,在PCB的焊接面也必須分布鉭電容﹑貼片電感等較高元件和細間距的SOIC﹑TSOP等器件,在此種情況下,只能采用雙面印刷焊膏貼片后回流焊接,而插件元件,應該在元件分布的盡可能集中,以適應手工焊接,另一種可能就是元件面的穿孔元件應盡可能分布在幾條主要的直線上,以適應最新的選擇性波峰焊接工藝,可以避免手工焊接而提高效率,并保證焊接質量。離散的焊點分布是選擇性波峰焊接的大忌,會成倍增加加工時間。
在印制板文件中對元器件的位置進行調整時,一定要注意元件和絲印符號一一對應,若移動了元件而沒有相應的移動該元件旁的絲印符號,將成為制造中的重大質量隱患,因為在實際生產中,絲印符號是具有指導生產作用的行業語言。
2.2 PCB上必須布置有用于自動化生產做必需的夾持邊﹑定位標記﹑工藝定位孔。
目前PCBA裝聯是自動化程度最高的行業之一,生產所使用的自動化設備均要求自動傳送PCB,這樣便要求在PCB的傳送方向(一般為長邊方向)上,上下各有一條不小于3-5mm寬的夾持邊,以利于自動傳送,避免靠近板子邊緣的元器件由于夾持無法自動裝聯。
定位標記的作用在于對于目前廣泛使用光學定位的裝聯設備,需要PCB提供至少兩到三個定位標記,以供光學識別系統對PCB進行準確定位并校正PCB的加工誤差。通常所使用的定位標記中,有兩個標記必須分布在PCB的對角線上。定位標記的選擇一般使用實心圓焊盤等標準圖形,為便于識別,在標記周圍應該有一塊沒有其它電路特征或標記的空曠區,尺寸最好不小于標記的直徑,標記距離板子邊緣應在5mm以上。
在PCB自身的制造中,以及在裝聯中的半自動插件﹑ICT測試等工序,需要PCB在邊角部位提供兩到三個定位孔。
2.3 合理使用拼板以提高生產效率和柔性。
在對外形尺寸較小或外形不規則的PCB進行裝聯時,會受到很多限制,所以一般采用拼板的方式來使幾個小的PCB拼接成合適尺寸的PCB進行裝聯,如圖5。一般單邊尺寸小于150mm的PCB,都可以考慮采用拼板方式,通過兩拼﹑三拼﹑四拼等,將大PCB的尺寸拼至合適的加工范圍,通常寬150mm~250mm,長250mm~350mm的PCB是自動化裝聯中比較合適的尺寸。
拼板設計可提高生產效率
另外一種拼板方式是將雙面都布置有SMD的PCB一正一反的拼成一個大板,這樣的拼板俗稱陰陽拼,一般是出于節約網板費用的考慮,即通過這樣的拼板,原來需要兩面網板,現在只需要開一面網板即可。另外技術人員在編制貼片機運行程序時,采用陰陽拼的PCB編程效率也更高。
拼板時子板之間的連接可以采用雙面對刻V型槽﹑長槽孔加圓孔等方式,但設計時一定要考慮盡可能使分離線在一條直線上,以利于最后的分板,同時還要考慮分離邊不可離PCB走線過近,而使分板時容易損傷PCB。
還有一種非常經濟的拼板,并不是指的對PCB進行拼板,而是對網板的網孔圖形進行拼板。隨著全自動焊膏印刷機的應用,目前較為先進的印刷機(比如DEK265)已經允許在尺寸為790×790mm的鋼網上,開設多面PCB的網孔圖形,可以做到一片鋼網用于多個產品的印刷,是一種非常節約成本的做法,尤其適合于產品特點為小批量多品種的廠家。
2.4 可測性設計的考慮
SMT的可測性設計主要是針對目前ICT裝備情況。將后期產品制造的測試問題在電路和表面安裝印制板SMB設計時就考慮進去。提高可測性設計要考慮工藝設計和電氣設計兩個方面的要求。
2.4.1 工藝設計的要求
定位的精度、基板制造程序、基板的大小、探針的類型都是影響探測可靠性的因素。
(1) 精確的定位孔。在基板上設定精確的定位孔,定位孔誤差應在±0.05mm以內,至少設置兩個定位孔,且距離愈遠愈好。采用非金屬化的定位孔,以減少焊錫鍍層的增厚而不能達到公差要求。如基板是整片制造后再分開測試,則定位孔就必須設在主板及各單獨的基板上。
(2) 測試點的直徑不小于0.4mm,相鄰測試點的間距最好在2.54mm以上,不要小于1.27mm。
(3) 在測試面不能放置高度超過*mm的元器件,過高的元器件將引起在線測試夾具探針對測試點的接觸不良。
(4) 最好將測試點放置在元器件周圍1.0mm以外,避免探針和元器件撞擊損傷。定位孔環狀周圍3.2mm以內,不可有元器件或測試點。
(5) 測試點不可設置在PCB邊緣5mm的范圍內,這5mm的空間用以保證夾具夾持。通常在輸送帶式的生產設備與SMT設備中也要求有同樣的工藝邊。
(6) 所有探測點最好鍍錫或選用質地較軟、易貫穿、不易氧化的金屬傳導物,以保證可靠接觸,延長探針的使用壽命。
(7) 測試點不可被阻焊劑或文字油墨覆蓋,否則將會縮小測試點的接觸面積,降低測試的可靠性。
2.4.2 電氣設計的要求
(1) 要求盡量將元件面的SMC/SMD的測試點通過過孔引到焊接面,過孔直徑應大于1mm。這樣可使在線測試采用單面針床來進行測試,從而降低了在線測試成本。
(2) 每個電氣節點都必須有一個測試點,每個IC必須有POWER及GROUND的測試點,且盡可能接近此元器件,最好在距離IC 2.54mm范圍內。
(3) 在電路的走線上設置測試點時,可將其寬度放大到40mil 寬。
(4) 將測試點均衡地分布在印制板上。如果探針集中在某一區域時,較高的壓力會使待測板或針床變形,進一步造成部分探針不能接觸到測試點。
(5) 電路板上的供電線路應分區域設置測試斷點,以便于電源去耦電容或電路板上的其它元器件出現對電源短路時,查找故障點更為快捷準確。設計斷點時,應考慮恢復測試斷點后的功率承載能力。
通過延伸線在元器件引線附近設置測試焊盤或利用過孔焊盤測試節點,測試節點嚴禁選在元器件的焊點上,這種測試可能使虛焊節點在探針壓力作用下擠壓到理想位置,從而使虛焊故障被掩蓋,發生所謂的“故障遮蔽效應”。由于探針因定位誤差引起的偏晃,可能使探針直接作用于元器件的端點或引腳上而造成元器件損壞。
3、結束語
以上是一些PCB設計時應考慮的主要原則,在面向PCBA裝聯的PCB可制造性設計中,還有相當多的細節要求,比如合理的安排與結構件的配合空間﹑合理的分布絲印的圖形和文字﹑恰當分布較重或發熱較大的器件的位置,在合適的位置設置測試點和測試空間﹑考慮在使用拉鉚﹑壓鉚工藝安裝聯接器等器件時,工模具與附近所分布元件的干涉等等,都是在PCB的設計階段所應該考慮的問題。一個優秀的PCB設計者,不但要考慮如何獲得良好的電性能和美觀布局,還有同樣重要的一點那就是PCB設計中的可制造性,以求高質量、高效率、低成本。
深圳宏力捷推薦服務:PCB設計打樣 | PCB抄板打樣 | PCB打樣&批量生產 | PCBA代工代料
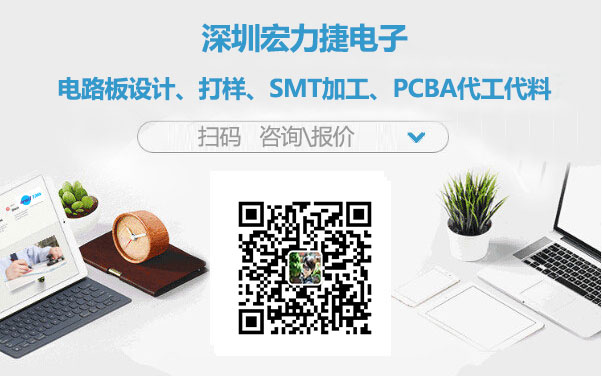