Past-In-Hole (通孔印錫膏PIH)就是把錫膏 (Solder paste) 直接印刷于 PCB (Print Circuit Board,電路板) 的電鍍通孔(PTH, Plating Through Hole)上面,然后再把傳統插件/通孔元件(DIP insert parts)直接插入已經印有錫膏的電鍍通孔里,這時電鍍通孔上的錫膏大部分會沾粘在插件零件的焊腳上,這些錫膏經過回流焊爐的高溫時會重新熔融,進而焊接零件于電路板上。
這種工法還有其他的名稱叫「引腳浸錫膏(pin-in-paste)」、「侵入式回流焊接 (intrusive reflow soldering)」 和「通孔回流焊(ROT, reflow of through-hole)」等。
這種工法的好處是可以免去手動焊接(hand soldering)或波焊(Wave Soldering) 的制程并進而節省作業工時(Labor),同時也可以提升焊接的品質,減少焊接短路(Solder short)的機會。
但這種工法卻有下列的先天限制:
1、傳統零件的耐熱能力必須符合回流焊的溫度要求。一般的插件零件通常使用比回流焊零件耐溫較低的材料。因為PIH工法要求傳統零件與一般的
SMT零件一起過回流焊(reflow),所以必須要符合reflow的耐溫需求。 無鉛的零件現在要求需可以耐到260°C維持10sec。
2、零件最好有卷帶包裝(tape-on-reel)而且有足夠的平面可以經由SMT的自動貼焊機(pick and place machine)來放到電路板(PCB)上,如果不行的話,就要考慮加派一名作業員,人工手動擺放零件,這時就要衡量所需的工時與品質不穩,因為人工插件有可能會因作業不小心而碰觸到其他已經擺放定位的零件。
3、零件body與PCB的焊墊要有standoff(架高)設計。一般PIH制程都會將錫膏印刷得比焊墊的外框還要大,這是為了增加錫膏焊錫量以達到75%的通孔填滿要求,如果零件與焊墊之間沒有standoff,過Reflow時熔融的錫膏會沿著零件與PCB之間的空隙游走,造成多余的錫扎渣與錫珠,影響日后的電氣品質。
4、傳統零件最好在第二面打件(如果有兩面SMT的時候)。零件如果已經先在第一面打件了,第二面繼續打SMD的時候,錫膏有可能會倒流進入傳統零件,造成零件內部短路的可能,尤其是連接器(connector)的零件更要特別小心。
另外,焊錫量是這種工法的最大挑戰。IPC-610對通孔焊接點的可接受標淮焊錫量必須大于載板厚度的75%以上,某些要求50%就可以了。(請參考下圖,詳細規格請查詢 IPC-610 section 7.5.5.1)
至于錫膏量的計算,可以用通孔的最大直徑減去引腳的最小直徑,然后乘上電路板的厚度取得,要記得再x2,因為錫膏內的助焊劑占了50%,也就是說經過reflow以后,也就是說錫膏的體積只會剩下到原來印刷錫膏的一半。
所需錫膏量體積 ≧ [(通孔的最大直徑 /2)2- 引腳的最小直徑/2)2]× π × 電路板的厚度 × 2
那要如何增加通孔的焊錫量呢?下面幾個方法提供給您參考:
1、在電路板的通孔(PTH)附近預留足夠的空間作 over print。
跟 Layout Engineer (
PCB布線工程師)討論,在需要 paste-in-hole 的通孔附近空出更多的空間印刷錫膏,也就是說附近盡量不要擺放其他的 pad(焊墊)或是其他不需要的焊接通孔,以避免 over print 時發生短路。
要注意的:錫膏印刷的平面空間無法無限度的往外延伸,必須要考慮到錫膏的內聚力能力,要不然錫膏會無法全部收回焊墊而形成錫珠。
另外也要考慮錫膏印刷的方向需配合焊墊延伸的方向。(有機會我們再討論這一點)
2、縮小電路板上通孔的直徑。
就如同上面的[所需錫膏量計算],通孔直徑越大,所需要的錫膏量也就越多,但同時要考慮的,通孔直徑縮得太小,零件就越南插入通孔。
3、采用 step-up(局部加厚) 或 step-down(局部打薄) stencil(鋼板)。
這種鋼板可以強迫局部增加錫膏的厚度,也就可以增加錫膏量,進而達到焊錫充滿通孔的目的,但這種鋼板平均比一般的鋼板要貴上約 10%左右。
4、調整適當的錫膏、印刷機的速度及壓力、刮刀的類型與角度等。
錫膏印刷機的這些參數或多或少都會影響到錫膏印刷量,另外 Viscosity(黏度)較低的錫膏其錫膏量會比較多一點。
5、加點錫膏。
可以考慮用點膠機(dispenser)加點錫膏于Paste-in-Hole的焊墊上來增加錫膏量,由于現今的SMT產線幾乎都已經沒有自動點膠機了,所以也可以考慮手動點膠,可是必須增加一名作業員的工時。
6、使用預成型錫片(solder preforms)
可以參考這篇文章:增加焊錫量的另一選擇 ─ Solder preforms (預成型錫片)
深圳宏力捷推薦服務:PCB設計打樣 | PCB抄板打樣 | PCB打樣&批量生產 | PCBA代工代料
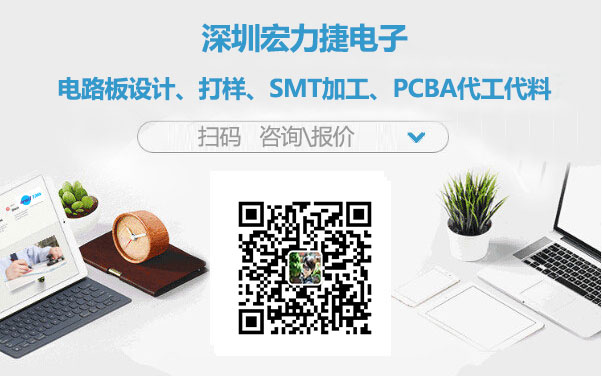