在珠江三角洲的
PCBA電子組裝生產環節中,因各個公司考慮設備成本.收益.折舊等投資收益問題,生產制造中
SMT生產常采用中低速貼片機;Bonding常采用工作臺旋轉的超聲波焊接機;THT常采用手工插件手工浸錫爐的生產方式來完成。這些混合組裝工藝對
PCBA設計的影響如下:
一、 單面或雙面布置SMT組件:
相當一部分塑料電子產品所使用的PCBA,混合使用了SMT .
COB . THT這三種電子組裝生產工藝,所以在設計為單面貼裝SMT組件時,采用這些設備和工藝都很實惠,能順利完成設計師的產品;設計為雙面生產SMT組件時,則需考慮三個方面:
1. 因受SMT設備影響,在其中一面布置的組件應盡可能的少,如不超過五個,則不需高成本的更改生產工序,也無需添加不同熔點的焊錫膏。具體生產方法為:
a.先正常貼裝零件少的一面,并回流焊接完成。
b.在另一面印焊錫膏,如使用機器印刷,則調整背面頂針位置;如使用手工印刷,需制作特殊夾具,使PCB平整,以保證錫膏印刷質量。
c.組件貼裝好之后,將PCB放在Bonding使用的大鋁盤上,進入回流焊機中,并適當調低底面溫度即可。
2. Bonding裸IC的正背面,需要留出20-30mm無SMT組件的空間,以給Bonding機的工作臺夾具留下空間(普通低端Bonding機是工作臺旋轉,裸IC的正背面必須對淮旋轉工作臺的軸心,才能獲得良好品質)。
3. 如果還需進行插件浸錫爐,這時對SMT組件的熱沖擊將超過每秒二百攝氏度以上,SMT組件會受到損壞。此時應盡量考慮SMT組件與THT組件分開布置在PCB的不同面。
二、PCB外形:
1. 一般為:
長:50mm---460mm 寬:30mm---400mm
生產最優選的PCB外形是:
長:100mm---400mm 寬:100mm---300mm
2.如PCB太小,應該制作成拼板,以便進行機器貼裝并提升貼片機效率。拼板需制作工藝邊(如無工藝邊,使用0805組件時,生產效率低,精度差,如使用0603組件則精度差到無法正常生產。)
3.工藝邊上需制作FIDUCIAL MARK:直徑為1mm至1.5mm的圓實心覆銅點。
三、拼板聯接:
1.
V-CUT聯接:使用分割機分割,這種分割方式斷面平滑,對后道工序無不良影響。
2.使用針孔(
郵票孔)聯接:需考慮斷裂后的毛刺,及是否影響COB工序的Bonding機上的夾具穩定工作,還應考慮是否影響插件過軌道,及是否影響裝配組裝。
四、PCB材質:
1.XXXP、FR2、FR3這類紙板PCB受溫度影響較大,因熱膨脹系數不同容易導致PCB上銅皮出現起泡、變形,斷裂,脫落現象。
2.G10、G11、FR4、FR5這類玻璃纖維板PCB受SMT溫度及COB、THT的溫度影響相對較小。
如果一塊PCB上需要進行兩種以上的COB. SMT. THT生產工藝,從兼顧質量和成本考慮,FR4適合大部分產品。
五、焊盤連接線的布線以及通孔位置對SMT生產的影響:
焊盤連接線的
布線以及通孔位置對SMT的焊接成品率有很大影響,因為不合適的焊盤連接線以及通孔可能起「偷竊」焊料的作用,在回流爐中把液態的焊料吸走(流體中的虹吸和毛細作用)。以下的情況對生產品質有好處:
1.減小焊盤連接線的寬度:
如果沒有電流承載容量和PCB制造尺寸的限制,焊盤連接線的最大寬度為0.4mm或1/2焊盤寬度,可以更小。
2.與大面積導電帶(如接地面,電源面)相連的焊盤之間最優選為用長度不小于0.5mm的窄連接線(寬度不大于0.4mm或寬度不大于1/2焊盤寬度) 。
3.避免連接線從旁邊或一個角引入焊盤。最優選為連接線從焊盤后部的中間進入。
4.通孔盡量避免放置在SMT組件的焊盤內或直接靠近焊盤。
原因是:焊盤內的通孔將吸引焊料進入孔中并使焊料離開焊點;直接靠近焊盤的孔,即使有完好的綠油保護(實際生產中,PCB來料中綠油印刷不精確的情況很多),也可能引起熱沉作用,會改變焊點浸潤速度,導致片式元器件出現立碑現象,嚴重時會阻礙焊點的正常形成。
通孔和焊盤之間的連接最優選為用長度不小于0.5mm的窄連接線(寬度不大于0.4mm或寬度不大于1/2焊盤寬度) 。
深圳宏力捷推薦服務:PCB設計打樣 | PCB抄板打樣 | PCB打樣&批量生產 | PCBA代工代料
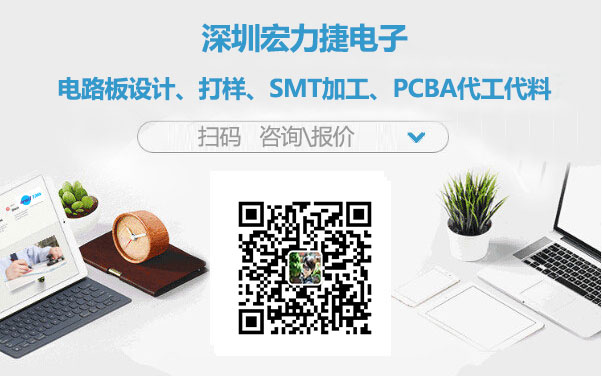